Is Your Business Ready For Fastening Process Monitoring And Control?
In the era of Industry 4.0, manufacturing processes are undergoing a dramatic transformation. The integration of the Internet of Things (IoT), Artificial Intelligence (AI), and smart technologies is reshaping how we monitor and control production lines. At the heart of this revolution lies a critical yet often overlooked component: the fastening systems.
In this blog, we explore the world of fastening process monitoring and control, and how advanced fastening technologies are enabling manufacturers to achieve increased levels of quality assurance.
What’s Fastening Process Monitoring and Fastening Process Control?
Fastening Process Monitoring
In a production line environment, monitoring a fastening process involves systematically checking each fastener installed in every application to ensure it meets specifications. For example, blind fastening tools with process monitoring can collect critical fastening data in real time and transmit it to a centralized IT system. This data may include:
- Pull force
- Distance
- Stroke
- Speed
- Current
- Bus voltage
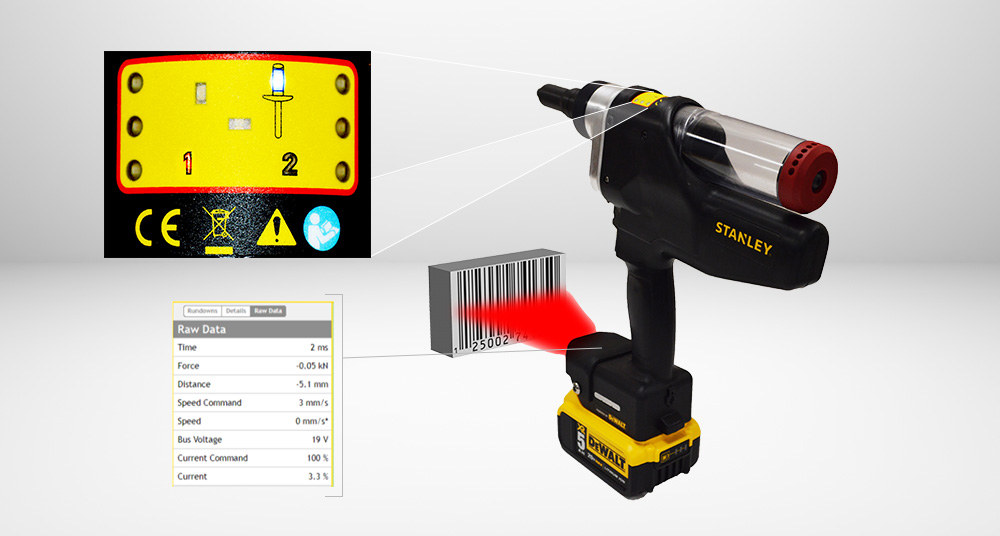
Visual lights on the BR12PP-8 tool indicate if the fastener has been placed correctly or not. This tool can also be connected to a controller into the manufacturing plant IT system to record real-time fastening data.
The error-proofing capabilities of these fastening systems provide immediate insights into the fastening process, allowing manufacturers to
- Identify non-compliant fasteners
- Remove defective components before they reach customers
- Ensure consistent quality
- Reduce the risk of fastening variability
- Prevent returns and recalls
Learn more about how an Italian Heat Pump Door Manufacturer reduced quality defects by 20% by adopting an advanced process monitoring system in their line.
Fastening Process Control
Process control in fastening refers to systems that manage fastening parameters before the actual assembly takes place. It focuses on controlling the process and setting fastening parameters before the operator places the fastener, ensuring it meets target specifications.
A great example is torque control for the installation of large threaded fasteners and it is especially critical in safety critical applications. Before initiating the fastening operation, the operator inputs specific parameters into the controllers, such as:
- Torque
- Angle
- Enable scanning – some tools are equipped with barcode scanning capabilities so the system can record the specific batch for which quality control has been performed
- Enable/disable specific tools connected to the controller
The threaded tool in operation will deliver precisely to those specifications, ensuring each fastener is installed according to the required standards. In most operations, controllers are easily visible to operators, allowing them to see in real-time if the torque they have just performed is OK or NOTOK according to their pre-determined specifications. Controllers can also be connected to conveyor systems and will prevent the product from moving to the next station until all torque operations have been performed correctly. Modern controllers are connected to centralized MES and QMS systems through different protocols including Open, Ethernet/IP, ProfiNet, ProfiBus, Devicenet, and can also be tailored to manufacturer's specific system requirements.
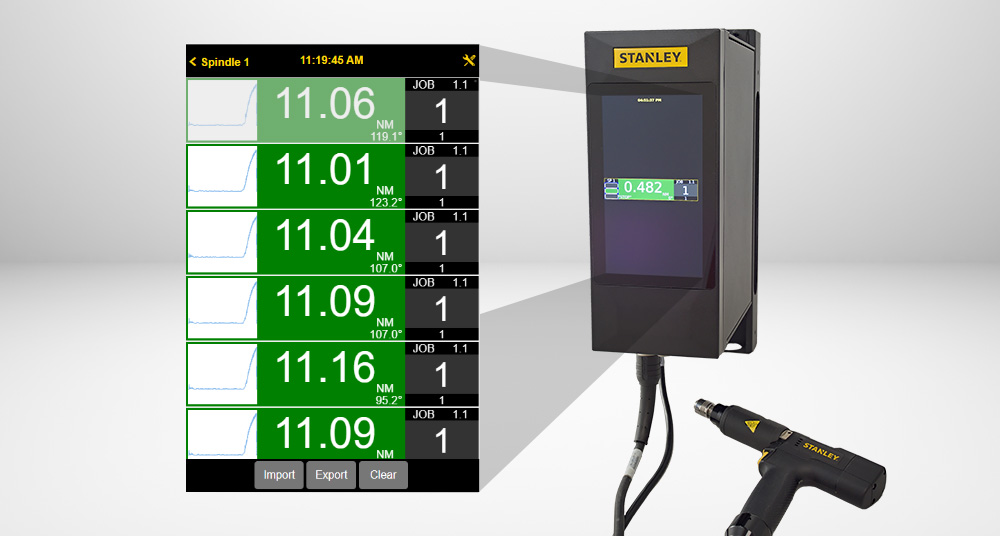
EB12P-1 Tool connected to a SC Controller for torque control. Color-coded feedback ensures thorough and accurate torque application. Torque OK (green) or Torque NOT OKAY (red).
By performing torque control in a threaded fastening operation, manufacturers benefit from:
- Ensuring proper tightening is performed, enhancing safety
- Improved quality control through visual feedback and data collection for each torque operation
- Increased traceability as collection in the MES ensures each torque history is recorded
- License-free ATB Alpha Toolbox software allowing for flexible tool management
- The ability to inspect torque curves, enabling deeper analysis and continuous improvement of the assembly process
Learn how a North American heavy machinery manufacturer enhanced the safety and quality of their braking system assembly by implementing precision torque control for air chamber fittings.
Can Fasteners Be Monitored and Controlled Simultaneously?
The quick answer is yes. Some fastening systems enable both process monitoring and control within the same operation. Stud welding systems , widely used in construction, serve as an excellent example of this capability.
Modern stud welding systems, equipped with microprocessors, collect data during the welding process, including:
- Weld current
- Arc voltage
- Lift movement
- Penetration depth
The stud welding system software compares the performance of each specific weld to an optimum weld profile. If the performed weld deviates significantly from the optimum, the system not only notifies the operator through signals or warnings but can also automatically adjust its settings to deliver optimal parameters for future welds.
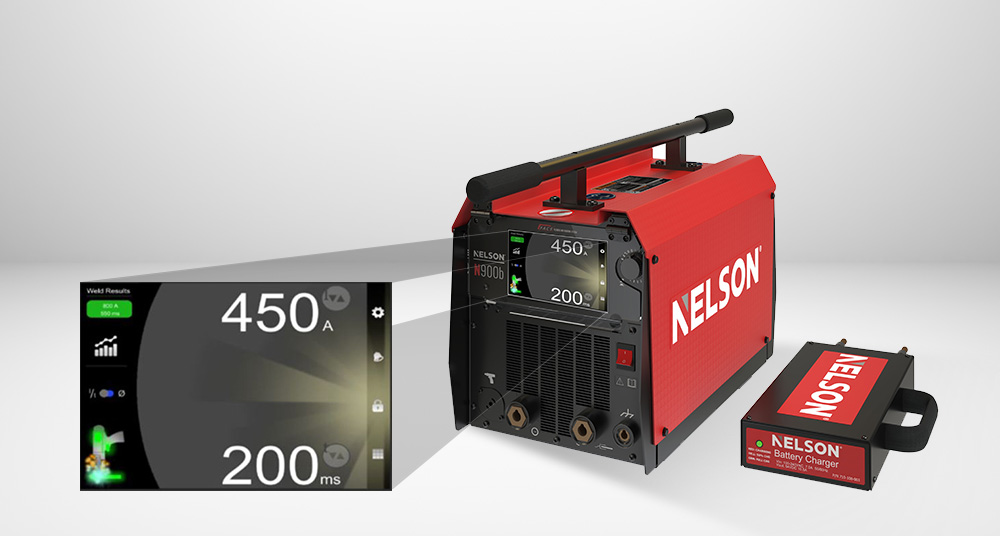
NELSON Stud Welding N900b with FACS system allow both process monitoring and control to deliver welding processes right to the desired specifications.
This dual functionality of monitoring and control ensures consistent quality and efficiency in the welding process. It saves time for the stud welding operator while providing peace of mind that each weld meets the highest standards.
As manufacturing evolves to the future, fastening process monitoring and control are becoming essential for businesses aiming to stay competitive. By embracing these advanced technologies, companies can ensure higher quality, improved efficiency, and enhanced traceability – key factors in determining if your business is truly ready for the future of manufacturing.