La sala de control virtual añade dimensión a los datos para el equipo de Warrington de STANLEY®
Lleve la productividad, los comentarios y la responsabilidad de la fábrica al infinito y más allá
Cuando el gerente de planta, Lee Birchall, necesita conocer el estado de cualquier elemento que se encuentre en el interior de su fábrica de 16.359 metros cuadrados de Warrington, en el noroeste de Inglaterra, no tiene más que consultar las dos pantallas que hay montadas en la sala de conferencias de la planta.
Como eje de la sala de control virtual de la planta, estas pantallas transmiten gran cantidad de información disponible en tiempo real sobre cada departamento involucrado en el flujo de trabajo en las instalaciones de Warrington, donde se fabrican elementos de fijación de una y dos piezas en múltiples líneas de productos de la marca. La sala de control, un caso de éxito de la Industria 4.0 y un avance de la fabricación digital implementado recientemente por STANLEY® Engineered Fastening, es "el centro neurálgico de la fábrica", según Birchall.
El concepto original de sala de control se lanzó en la planta hace 11 años. Entonces, como ahora, el personal clave se reunía dos veces al día para revisar el ritmo de producción, identificar problemas potenciales y priorizar la carga de trabajo, todo con el objetivo de usar esta información para impulsar de forma proactiva la satisfacción del cliente, aprovechar las eficiencias para controlar los costes del cliente y fomentar la resolución creativa de problemas. Sin embargo, la representación original de los números en los que se basaron estas reuniones resultó ser poco flexible y pronto quedó obsoleta. "Era una amalgama de datos", dice Paul Atherton, gerente sénior de RR. HH. de STANLEY® Engineered Fastening de Reino Unido y Países Bajos. "Aunque las reuniones siempre eran impactantes en términos de trabajo en equipo y resultados, con la solución anterior era muy fácil acabar perdiéndose entre números. Ahora todo tiene mucho más sentido".
La sala de control virtual proporciona parámetros personalizados, monitorización en tiempo real y retroalimentación positiva.—Lee Birchall, director general, planta de Warrington
STANLEY® Engineered Fastening
Birchall coincide. "Lo que pretendíamos al trasladar las reuniones al formato digital era mantener el mismo espíritu y los mismos resultados. La sala de control virtual permite justamente eso, además de proporcionar parámetros personalizados, monitorización en tiempo real y retroalimentación positiva", afirma. "Es una práctica recomendada en consonancia con la industria 4.0, el pilar de excelencia digital de SFS 2.0 y la metodología de las fábricas inteligentes".
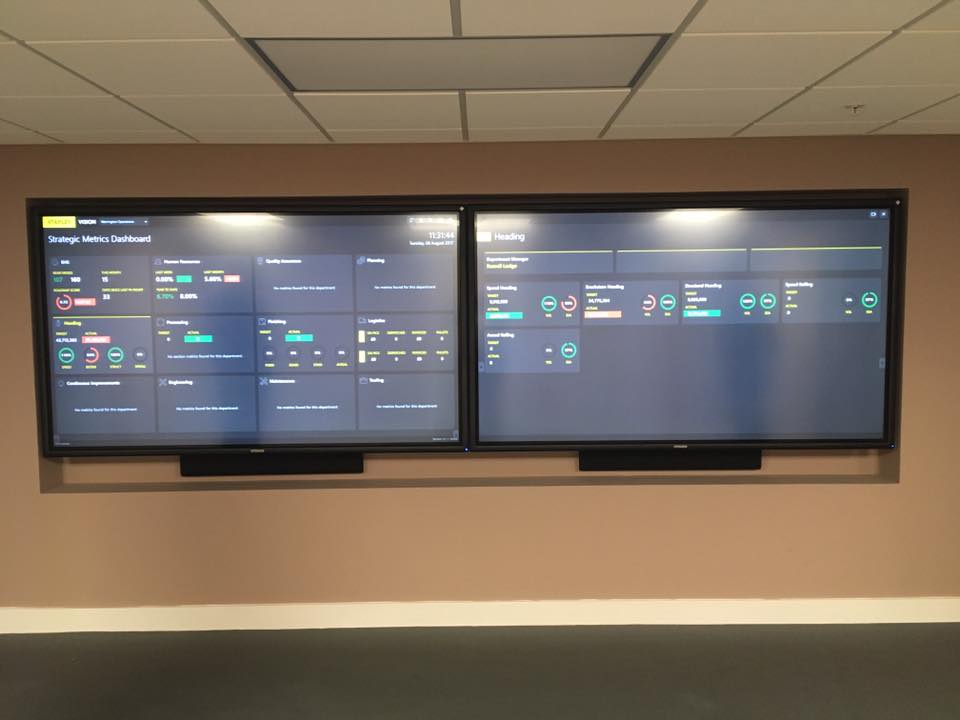
El sistema virtual, lanzado en septiembre de 2017, integra todas las funciones esenciales de la fábrica e informa, no solo sobre estadísticas de fabricación y producción, sino también sobre salud y seguridad, recursos humanos y calidad. También se utiliza de forma interactiva para otras aplicaciones como la formación; por ejemplo, el sistema se puede utilizar para administrar "charlas informativas" con los empleados, con firmas digitales que se utilizan para registrar la participación y el cumplimiento. Además de números, proporciona completas herramientas de visualización de datos que permiten obtener una visión global de todos los parámetros de un vistazo. Además, se han eliminado las demoras en los informes: el personal de toda la planta utiliza tabletas para registrar números, de manera que los datos se actualizan constantemente. Todo esto hace que los niveles de calidad y producción de Warrington alcancen constantemente nuevos niveles: Muy pronto, la planta alcanzará los 1100 millones de elementos de fijación fabricados.
Una ventaja más difícil de cuantificar, pero igualmente útil es la información interdepartamental que proporciona. "Para mí, esto no solo ha hecho que sea mucho más fácil asimilar la información, ya que realmente puedes experimentar los datos, sino que ha sido una excelente oportunidad de aprendizaje", dice Joann Hepburn, asesora de RR. HH. "Desde la perspectiva de alguien que no trabaja en el taller, la sala de control virtual es como una ventana que me permite ver lo que sucede en departamentos. De hecho, me hace sentir parte del equipo".
Pero la verdadera revelación del sistema, según los jefes de departamento, es la cantidad de retroalimentación positiva que ofrece, lo que facilita la resolución creativa de problemas en cada reunión y permite superar las expectativas del cliente. "Dado que trabajamos muy de cerca con nuestro desarrollador de software, podemos recabar todas las sugerencias de los empleados e incorporarlas al sistema y mostrar los resultados en apenas uno o dos días", explica Birchall. "Pero con la amalgama de datos de antes, esto era imposible." Además, todos los miembros de nuestro equipo tienen facultad para mejorar el sistema. La flexibilidad de este sistema proporciona un nivel de rendimiento superior".
Realmente puedes experimentar los datos.—Joann Hepburn, asesora de RR. HH., planta de Warrington
STANLEY® Engineered Fastening
La forma en que se originó esa capacidad de respuesta es una prueba de la responsabilidad de toda la división en cuanto a "clientes, compañeros de trabajo y comunidades". El desarrollador de software al que hace referencia Birchall es Ryan Kenny, quien comenzó en la empresa cuando tenía solo 15 años como parte de unas prácticas de formación en datos digitales no remuneradas a través de la universidad local. Ahora, como analista de sistemas comerciales a tiempo completo en la empresa, el software de Kenny está listo para implementarse a nivel mundial en nuestras instalaciones de todo el mundo.
¿Qué es lo próximo para el equipo? A Birchall le entusiasma presentar la sala de control virtual a todos los empleados de la planta. Al final del día, este entusiasmo se traducirá en más ideas para mejorar el rendimiento, lo que a su vez beneficiará a los clientes de la empresa. Cuando Lee Birchall sume todos los datos de las dos pantallas de su sala de conferencias, esa será la ecuación final: muchos, muchísimos clientes satisfechos.
30 de marzo de 2018