How Battery Powered Rivet Guns Increase Efficiency and Reduce Fatigue in Ground Transportation
Around the world, demand is increasing for every category of ground transportation. Both the freight and passenger railcar market and the bus market have a projected CAGR of 8% between now and 2026. Several factors are driving this growth, but increased urbanization and focus on efficiency and sustainability are at the top. As the ground transportation industry becomes more focused on reducing emissions, those concerns have come home to bus, rail, coach, and trailer manufacturers. One of the most effective ways the manufacturing sector can increase efficiency in production is also one of the simplest: shifting to battery-powered hand tools.
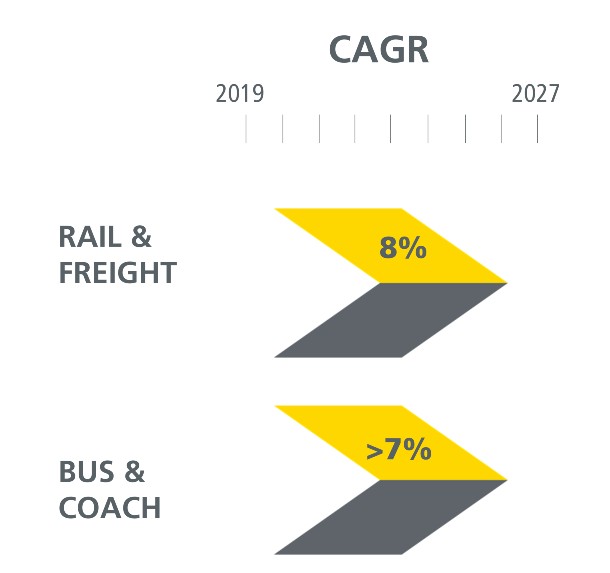
A New Generation of Tools Offers New Solutions
In the past, pneumatically-driven hand tools were the industry standard in manufacturing; they delivered the consistency and power needed for production. But a new generation of cordless hand tools is changing the game and leading some manufacturers to rethink their operations. The electric tool market is delivering lighter, more powerful cordless hand tools than ever before, with long-lasting batteries that make them suitable for production lines.
In ground transportation manufacturing, the rivet gun is the most important player on the assembly line. And up until now, air-driven rivet guns have been the go-to for production lines, despite several of their unavoidable inefficiencies. Currently, the development of powerful battery-operated tools in conjunction with a sharp focus on energy-saving initiatives is paving the way for a massive shift in the manufacturing sector.
Cost Efficiency of Battery-Powered vs. Pneumatic Riveting Guns
There are a few key reasons why cordless hand tools increase cost-efficiency in manufacturing operations. Motor-driven tools require almost no maintenance costs, and their energy-efficiency saves energy that might be wasted by pneumatic tools. In contrast, maintaining a reasonable level of efficiency in an air-powered system requires a significant amount of monitoring and maintenance.
Despite their reputation for offering consistent power and reliability, air-driven tools deliver these benefits at a steep price. Production facilities consume up to 10% of their total electricity expenditures powering air compressors. Worse yet, on average, 30% of the compressed air leaks out without ever being used. That means that operators are losing money every minute that a pneumatic system is running. In terms of sheer efficiency, studies have shown that air driven tools use around seven to thirteen times more energy to run than their battery-operated counterparts. The ROI on transitioning from pneumatic to battery-powered tools is around 17.3%, making the shift economically sensible.
User Experience of Battery-Powered Riveting Guns
In addition to being more energy-efficient, using cordless riveting guns also reduces the risk of workplace safety incidents caused by the hoses attached to air-driven tools. Cutting down on both the liability and expensive payouts posed by workplace injuries represents significant cost benefits.
Perhaps the most overlooked area of increased efficiency battery-operated riveting tools offer is their impact on their users’ bodies. In the manufacturing sector, tool operators generally spend hours at a time performing repetitive motions. Pneumatic riveting guns sometimes force operators to “fight” with air hoses to get the right angle of operation. Cordless hand tools offer improved ergonomics, allowing users to maneuver in all directions without having to negotiate with an air hose. Studies also suggest cordless tools reduce the demands on the forearms during use, resulting in less fatigue and fewer repetitive motion injuries.
Production Efficiency in Battery-Powered Riveting Tools
Cordless riveting tools offer several production advantages. In applications where access to a power source is limited, such as in remote solar installations, battery-powered riveting tools allow operators to work without the need for heavy generators. In a production facility, the lack of air lines lets operators move more freely on the floor and switch between tools quickly and easily.
But without question, one of the most useful features battery-powered tools offer is the use of SMART features. Process monitoring, programmable functions, and digital performance tracking increase confidence and work quality. Operators receive alerts when fasteners aren’t properly tightened, and process monitoring makes it easy to locate faulty rivets—ensuring consistent quality and reducing manufacturing defects.
Transitioning from pneumatic to battery-powered riveting tools offers energy efficiency, improved user experience, and production benefits. We have been providing tools for manufacturers for decades and is the largest and most innovative battery tool organization in the world. We’ve been developing, engineering, and manufacturing right alongside the industries who rely on us for tools they can trust. Contact us today to discuss how your ground transportation operation can benefit from shifting to battery-operated riveting tools.