La salle de contrôle virtuelle ajoute une dimension aux données qu’exploite l’équipe STANLEY® Warrington
La productivité, le retour d’information et la responsabilité de l’usine sont poussés à l’infini et au-delà
Lorsque le directeur général de l'usine, Lee Birchall, a besoin de connaître l’état d’un élément des murs de son usine de 16,35 mètres carrés (176 000 pieds carrés) à Warrington, dans le nord-ouest de l'Angleterre, il lui suffit de consulter deux écrans installés dans la salle de conférence de l’usine.
Véritable pivot de la salle de contrôle virtuelle de l’usine, ces écrans diffusent une multitude d’informations disponibles en temps réel concernant chaque service impliqué dans le flux de travail de l’usine de Warrington, qui fabrique des fixations à une ou deux pièces dans plusieurs gammes de produits. La salle de contrôle, belle réussite de l’équipe Industry 4.0 qui constitue une avancée dans le processus de fabrication numérique récemment mis en œuvre par STANLEY® Engineered Fastening, est le « centre vivant et dynamique de l’usine », selon Birchall.
L’originalité du concept d’une salle de contrôle a été lancée à l’usine il y a 11 ans. À l’époque comme aujourd'hui, le personnel clé se réunissait deux fois par jour pour prendre le pouls de la production, cerner d’éventuels problèmes et établir des priorités dans la charge de travail - tout cela dans le but d’utiliser les données pour améliorer de manière proactive la satisfaction des clients, tirer parti de l’efficacité pour contrôler les coûts des clients et promouvoir la résolution créative des problèmes. Mais la scénographie originale des chiffres sur laquelle ces réunions étaient basées était rigide et elle devint rapidement inadaptée. « Il s’agissait d’un océan de tableaux blancs », déclare Paul Atherton, directeur des ressources humaines chez STANLEY® Engineered Fastening, Royaume-Uni et Pays-Bas. « Si les réunions impactaient systématiquement le travail d’équipe et les résultats, avec la solution précédente, il était très facile de se perdre dans les chiffres. Désormais, les chiffres sont nettement plus sensés. »
La salle de contrôle virtuelle permet d’obtenir des mesures personnalisées, un suivi en temps réel et un retour d’information positif.–Lee Birchall, directeur général, usine de Warrington
STANLEY® Engineered Fastening
Birchall partage cet avis. « En organisant des réunions virtuelles, nous voulions conserver la même philosophie et les mêmes résultats. La salle de contrôle virtuelle le fait, justement, en nous permettant également d’obtenir des mesures personnalisées, un suivi en temps réel et un retour d’information positif », explique-t-il. « Il s’agit d’une bonne exemplaire qui cadre avec les principes de l’équipe Industry 4.0, du fondement de l’excellence numérique SFS 2.0 et de la méthodologie de l’usine SMART. »
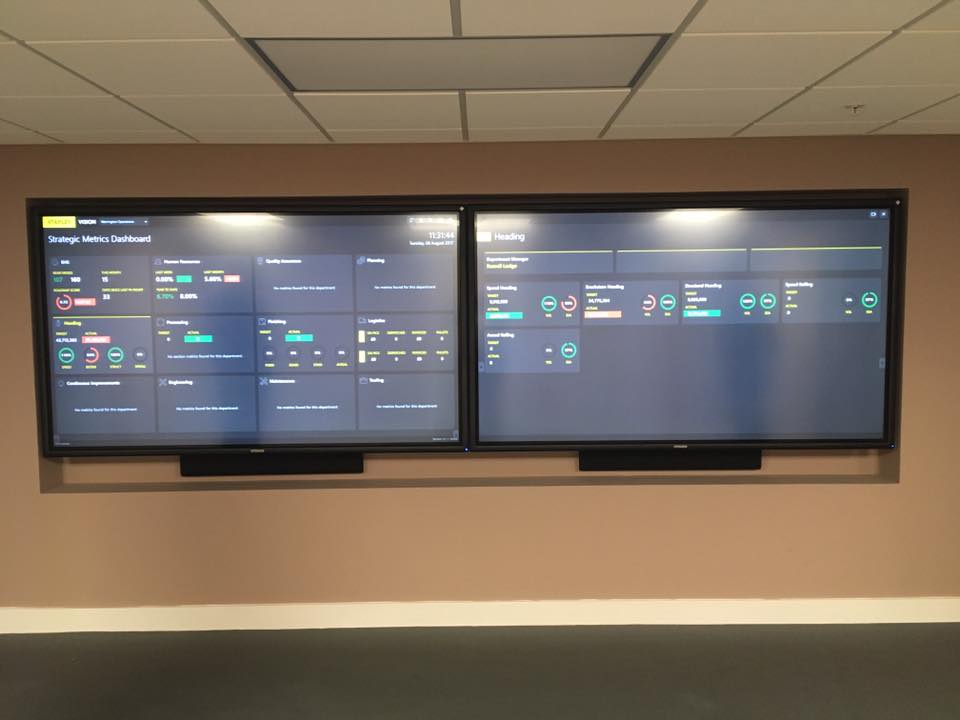
Lancé en septembre 2017, le système virtuel intègre toutes les fonctions essentielles de l’usine, et communique non seulement des statistiques relatives à la fabrication et la production, mais aussi à la santé et la sécurité, les ressources humaines et la qualité. Il est également utilisé sur une base interactive pour des applications telles que la formation - par exemple, le système peut être utilisé pour organiser de « brèves discussions informelles » avec les employés, en ayant recours aux signatures numériques pour enregistrer la participation et le respect des dispositions. Il fournit non seulement des chiffres, mais aussi des outils de visualisation des données, ce qui permet d’assimiler les mesures d’un seul coup d’œil. De plus, il n’existe pas de décalage dans la présentation des rapports : dans toute l’usine, le personnel utilise des tablettes pour saisir les chiffres, de sorte que les données sont constamment actualisées. Tout cela fait que les niveaux de qualité et de production de Warrington atteignent constamment de nouveaux sommets : la production de l’usine pourra bientôt atteindre 1,1 milliard de fixations.
Un avantage moins facile à mesurer, mais tout aussi important, du système est qu’il permet de visualiser les différents services. « Pour moi, non seulement cela facilite l’assimilation des informations – vous pouvez vraiment expérimenter les données – mais il s’agit aussi d’une excellente occasion d’apprentissage », déclare Joann Hepburn, conseillère en RH. « Du point de vue de quelqu’un qui ne travaille pas dans l’atelier, la salle de contrôle virtuelle m’offre un meilleur aperçu des activités des autres services. J’ai l’impression d’être un membre à part entière de l’équipe. »
Mais la véritable révélation du système, selon les chefs de service, a été le nombre de retours positifs que le système permet, facilitant ainsi la résolution créative des problèmes dans le but de satisfaire et de dépasser les attentes des clients. « Comme nous travaillons en étroite collaboration avec notre développeur de logiciels, nous pouvons prendre les suggestions des employés, les intégrer dans le système et obtenir des résultats en un ou deux jours », explique Birchall. « Cela n’était pas possible dans l’océan de tableaux blancs. » De plus, chaque membre de notre équipe est habilité à améliorer le système. La souplesse de ce système procure de plus grandes performances. »
Vous pouvez vraiment expérimenter les données.–Joann Hepburn, conseillère en RH, usine
STANLEY® Engineered Fastening de Warrington
Les raisons de cette réactivité témoignent de la responsabilité dont font preuve nos « clients, collègues, communautés » à l’échelle de la division. Le développeur de logiciels auquel Birchall fait référence est Ryan Kenny, qui a intégré l’entreprise à l’âge de 15 ans dans le cadre d’une formation en alternance non rémunérée sur les données numériques dispensée par l’université locale. Alors qu’il travaille actuellement comme analyste des systèmes informatiques à temps plein au sein de l’entreprise, le logiciel de Kenny devrait être mis en œuvre dans nos installations du monde entier.
Quel avenir pour l’équipe ? Birchall est ravi de présenter la salle de contrôle virtuelle à l’ensemble des employés de l’usine. Au bout du compte, cet enthousiasme permettra sans aucun doute de transposer un plus grand nombre de propositions d’amélioration des performances, ce qui profitera aux clients de l’entreprise. Lorsque Lee Birchall additionne toutes les données sur les deux écrans de sa salle de conférence, l’équation finale est la suivante : un plus grand nombre de clients satisfaits.
30 mars 2018